The idea of continuous improvement is probably as old as humankind, but it was Toyota who popularized the concept of Kaizen and Lean manufacturing. The idea of Lean manufacturing is to maximize customer value while minimizing waste. Simply, Lean means creating more value for customers with fewer resources.
The principles behind this process allowed Toyota to maintain both quality and flexibility while growing to become one of the largest car manufacturers in the world.
A Lean organisation, such as Toyota, understands and focuses on increasing customer value, using the concept of Kaizen. The idea of Kaizen, or continuous improvement, is to use your creativity to react to and solve problems, identify clever solutions, and then share solutions with the rest of your team – creating an ever learning, ever improving organisation. The ultimate goal is to create perfect customer value using processes with zero waste.
For instance, in sectors like manufacturing, organizations can significantly benefit from learning content management systems for manufacturing, which streamline the distribution and management of training content, ensuring that best practices and compliance are consistently applied across all levels of production. This is crucial for maintaining safety and efficiency on the production floor.
Implementing Lean processes means optimizing the flow of products through the entire value stream by eliminating waste where possible. Lean processes need less human effort, less capital, and less time to create customer value. In addition, Lean processes are flexible and can quickly respond to change in customer demand.
A common misconception is that Lean is only for manufacturing. Not true. Lean applies to every business and process, and can even be used in your personal life. Lean is a way of thinking rather than a set of tools and techniques, even if there are important tools and techniques within Lean.
How can you apply the principles of Lean manufacturing and Kaizen to technical writing and documentation? In this post, I break down the principles into the following three steps, and describe how they are applicable to today’s documentation managers and content strategists:
- Define value from your customer's perspective.
- Learn to see waste.
- Make a two-second improvement every day.
1. Define value from your customer's perspective.
To determine if something adds value you must take your customer's perspective. This is key to eliminating waste and maximizing value.
If your customer doesn't care about X, Y, or Z, it doesn't have to be included in your documentation.
Figuring out what your customer cares about is essentially a process of user experience research. Working with the UX team or the support department can get you a long way to getting to know your customers.
Generally speaking, users value documentation that is easy to find, easy to use, and easy to understand, filling the intersection of “what users need to do”, and “what users can’t figure out on their own”:
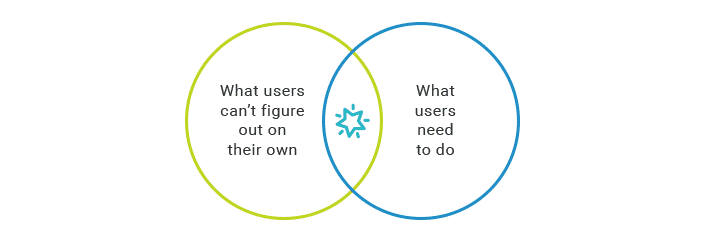
2. Learn to see waste.
Learning to see waste is another key aspect. In lean manufacturing, there are three main types of waste:
- Overburdening – causing unnecessary stress to people and processes. This can be caused by non-value adding activities, and other types of problems such as lack of training, unclear ways of working, or the wrong tools.
- Variation - unevenness or inconsistency caused by uneven demand levels.
- Non-value adding activities - any activity or process that does not add value; a waste of your time, resources, and money.
Overburdening and variation are important types of waste, but it is easier to identify waste in the form of non-value adding activities. The non-value adding activities are further divided into seven subcategories of waste:
- Overproduction
- Over processing
- Transportation
- Inventory
- Motion
- Defects
- Waiting
Let's look more closely at the seven wastes, and how each can be addressed with Flare.
Overproduction
Overproduction results in producing more than the customer requires. In terms of technical information, this can be compared to the content that cannot be used to achieve user goals, such as unnecessary background information. One example of overproduction is a chapter on “The History of Money” in a user manual on portfolio management software. While informative, the chapter is not directly related to the purpose of the document.
With Flare, you can avoid overproduction by using snippets to single source content. This is one of the key advantages of Flare. A snippet is file used for single-sourcing that acts sort of like a miniature topic. In a snippet, you can insert and format text, tables, pictures, and whatever else can be included in a normal topic. A snippet can be inserted into one or more topics throughout your project. You can even insert them into other snippets, creating nested snippets.
Over processing
Over processing means that you are working on something more than necessary. For example, try reading the following text:
Aoccdrnig to rscheearch, it deosn't mttaer in waht oredr the ltteers in a wrod are, the olny iprmoetnt tihng is taht the frist and lsat ltteer be at the rghit pclae. The rset can be a toatl mses and you can sitll raed it wouthit a porbelm. Tihs is bcuseae the huamn mnid deos not raed ervey lteter by istlef, but the wrod as a wlohe.
Now, does this mean that spell-checking is over processing? Probably not, but it makes you think. Are you processing each topic too much?
By using Flare's Spell Check and Text Analysis tool - you can quickly gauge the quality of a topic, and make sure the content is high quality without doing much manual work. Running the Text Analysis tool can give you an idea of how easy or difficult it is to read your content. Scores are based on “The Flesch Reading Ease” and “Flesch-Kincaid Grade Level” tests. The “Flesch Reading Ease” generates a score between 1 and 100 that roughly correlates to how easy or difficult it is to read the text. The higher the score, the easier it is to read the content. And if the score is low, the harder it is to read.
Transportation
In the world of information, transportation translates to conversion. For example - converting information from one format to another.
Using Flare's Word or Excel import is a great example of reducing the waste of transportation by means of automation. The Kaizen Plugin's Data Import tool is another example.
With Flare’s Word import feature – you can convert your legacy documentation to proper Flare topics in a just a few clicks. For more information, see Flare’s help topic on Importing Word Files.
With Flare’s Excel import feature you can import tables from Excel to topics or snippets. For more information, see Flare’s help topic on Importing Excel Files.
Alternatively, with the Kaizen Plugin’s Data Import feature, you can create topics from rows in a spreadsheet. For example, you can use the feature to create two topics from the following spreadsheet:
You can also use the Kaizen Plugin’s Data Import feature to import more advanced data sets from .xls or .csv files you have exported from your ERP, CRM, or issue tracking system, such as Jira.
Inventory
Inventory is just a pile of unfinished products. For example, you might have ten unfinished topics that are not yet adding value for customers. Working on many things at the same time often leads to inventory, and is the reason why it often makes more sense to work on fewer things from start to finish, instead of doing batch work - the concept of limiting work in progress.
Using MadCap Central’s Tasks feature to manage your tasks and projects can help you make sure you're not doing too much work at once. In MadCap Central, you can also create project and generic checklists to keep track of work related to your uploaded Flare projects. Using the Kanban TOC method along with The Kaizen Plugin's TODO notes is another approach.
Motion
Motion translates to searching for tools and information. If a tool is more than a few clicks away, you probably need to move it closer. The analogy is that in a factory, if you need to unnecessarily move to find tools, or to assemble a product, that movement equates to waste.
Automating certain tasks so that you don't have to do them manually is a great way to reduce motion. For example, using Flare's keyboard shortcuts, macros, repeat last action shortcut, template snippets, or the Kaizen Plugin - you can reduce a lot of motion in the sense that you can accomplish tasks with fewer clicks.
Learn more about Flare’s keyboard shortcuts and creating custom macros in Flare’s online Help.
Defects
Defective products have to be re-processed, going through each step of the process again, which results in additional time and effort dedicated to the process.
Using MadCap Analyzer will help you reduce defective work in Flare and also optimize your content. With Analyzer, you can scan for:
- Broken internal and external links
- Unused content files including topics and images
- Snippet and Variable candidates
- Topics not in a TOC or Index
- New style suggestions
- And more
Waiting
For all tech writers I know, waiting for information or reviews from subject matter experts (SMEs) is the single biggest waste they experience. Working to eliminate waste in SME reviews is a key to success. A big factor in making this successful is to simplify the review process as much as possible.
Using Flare's Contributor tool can help you streamline your review process. Subject Matter Experts can use Contributor to review, edit, or create new topics for the Flare authors to incorporate into the source content. If you turn on track changes in Flare, you can create a Word document or a PDF with those changes and comments preserved. Another approach is to use the Quick PDF feature in the Kaizen Plugin to quickly generate a PDF you can send along for review to your developers, saving time and frustration in the process.
3. Make a two-second improvement every day
By thinking about what your customers value, and by learning to see in-process waste, you are empowered to make and share daily two-second improvements – getting more done with less effort.
I propose that you spend as much as 30 minutes every day to improve a task by two seconds. Shaving off two seconds on a task that you do five times a day will save you 40 minutes in a year. The net gain is 10 minutes, creating a return-on-investment of 33%. If you then share your improvement with a colleague – the time saving is 40 minutes, but the initial investment only a few minutes. Sharing improvements within a team is where the magic happens, and can result in massive gains. For example, at Toyota, employees generate more than a million improvement ideas every year, and 90 percent of those ideas are implemented and shared – increasing the customer value every year.
It could be as simple as learning a few keyboard shortcuts, or as advanced as setting up automated data imports from your ERP system to automatically create release note topics.
So, what can you improve? Go ahead and share your improvements in the MadCap Flare user group on LinkedIn or in the friendly Slack channel for Flare users.